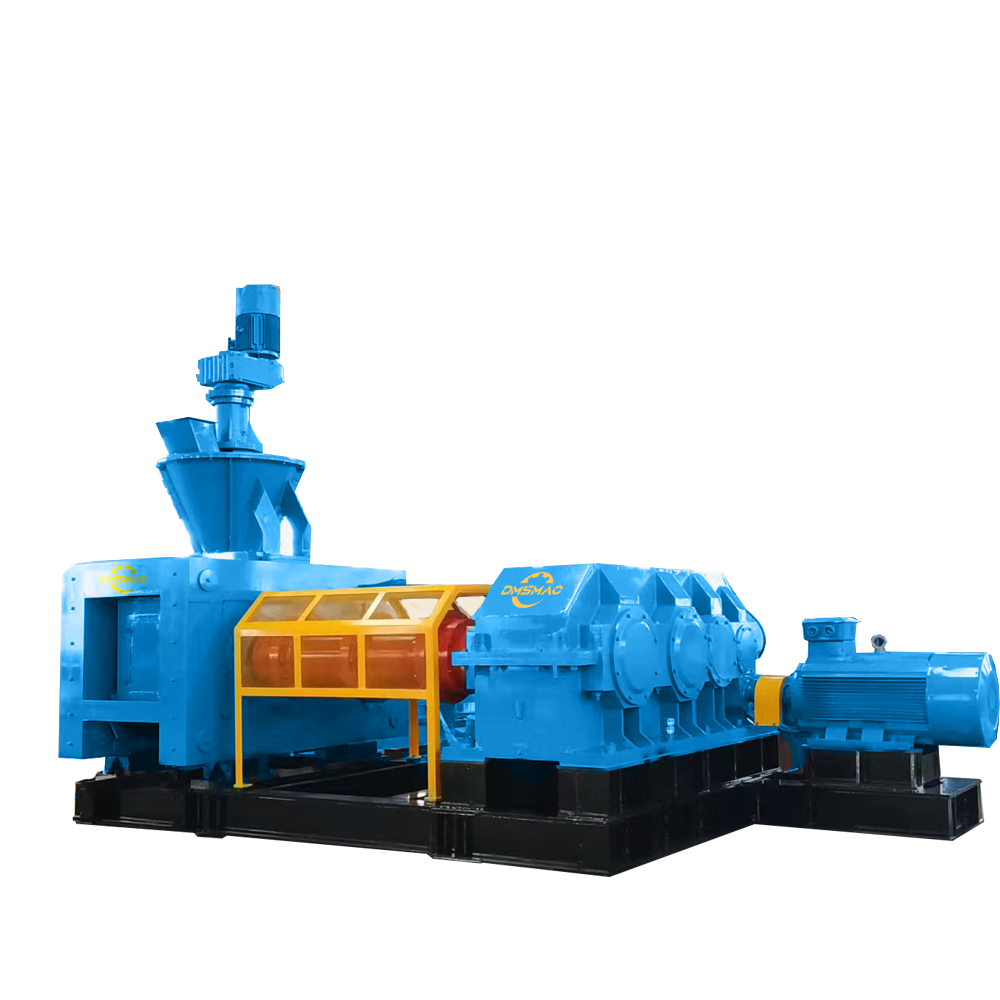
Briquette Machine Without Adhesives
Production Capacity: 1000-50000 kgs Per Hour
Application: Press materials into briquettes without adhesive and water by super high power, such as Coal, mining, metallurgy, refractory materials, chemical industry, building materials and other industries.
Briquette Shape and Size:Oval,Square,Pillow Shape & Customizable 15mm-100mm
Features:
- Stable speed, high molding rate, uniform briquette size;
- Higher, adjustable molding pressure for improved product quality.
- Safe, reliable molding system with easy-to-replace parts and low maintenance.
- The structure is simple and compact, saving space.
- Smooth demoulding, low noise and less dust;
- PDF DOWNLOAD
1. What is briquette machine without adhesives?
Briquette Machine without Adhesives, named high pressure briquette machine, dry powder briquette machine, is a kind of equipment that presses powdered raw materials into briquette without adhesives, the purpose of which is to reduce dust, increase bulk density, return for use, improve transportation characteristics, etc.
2. Where is application of Briquette Machine without Adhesives:
For powder materials that cannot come into contact with water or do not require adhesives, as well as materials that require high hardness of the finished briquettes, briquette machine without adhesive can be considered. Due to the high forming efficiency of the riquette machine without adhesive and the high strength and density of the finished briquettes, it is not easy to break or fall off, and the finished briquettes are stable; and the high degree of automation of the riquette machine without adhesive is widely used in the metallurgical field, chemical industry, organic fertilizer/inorganic fertilizer granulation, environmental protection industry, and building materials industry, etc.
Metallurgical industry:Waste recycling: Processing metallurgical waste such as steel slag, iron ore powder, aluminum ash powder, silicon manganese ore powder, etc., by pressing them into ball blanks as smelting raw materials, improving the utilization rate of waste; processing metal waste such as iron filings and aluminum powder to improve recycling efficiency.
Auxiliary material molding: Press auxiliary materials such as oxidized iron sheets, dust removal ash, and pool mud into high-density pellets for direct furnace smelting.
Chemical industry: Pressing powdered materials such as coal powder, coke, activated carbon, fertilizer, etc. to improve transportation and combustion performance;
Environmental protection: Reducing dust pollution by wrapping harmful substances, such as treating aluminum ash, sludge, pond mud, tailings and other industrial solid wastes, and realizing resource utilization after pressing;
Coal industry: Pressing bulk materials such as lignite and coal powder into regular pellets to improve combustion efficiency and reduce transportation losses; Pressing fuels such as coking coal and coke dust to improve energy utilization and storage convenience;
Refractory industry: Processing refractory powders such as magnesia, bauxite, dolomite, etc. to make high-strength pellets for high-temperature industrial scenarios;
Building materials and other industries: Pressing non-metallic minerals such as gypsum and tailings for building materials production or secondary processing;
3. How is the briquette machine withtout adhesive working?
When the equipment is running, material is fed evenly and in equal amounts from the top of the equipment, and the material is forced to be discharged through the spiral pre-pressing device, and then enters the two horizontal pressing rollers. The two rollers are driven by the reducer and rotate in opposite directions at the same speed. At the same time, the material is forced to be fed between the two rollers. By adjusting the rotation of the main shaft, the space above the two rollers is always filled with materials.
The briquettes socket on the surface of the roller is in an open state to bite into the material. As the roller rotates, the ball socket enters a closed state to compress the material (also known as re-exhaust), and then the ball socket is in an open state again and is compressed into the briquette. At this time, the briquette will naturally fall out of the mold due to the unbalanced force, the elasticity of the briquette and the effect of gravity. The whole process can increase the density of the materials by 1-3 times, thereby achieving the required strength.
In the process of pressing , the quantitative feeding of the materials is very important, so a quantitative feeding device is often set up in the front process of the briquette press. After pressing the briquette, due to the presence of small particles, screening is very necessary. Therefore, the balls produced often have to pass through a screening device, which can be simple, such as a fixed screen, or a motor-driven screening machine.The screened materials need to re-enter the entire system for re-molding, and this entire system constitutes the lime molding process.
In addition to providing a complete set of briquette making process, DMSMAC can also provide various equipment, feeding and discharging systems customized according to customer needs, docking with on-site raw material systems and dust removal systems, or provide a complete set of PLC systems and corresponding solutions
Take Lime press system as sample:
4. Components Of Briquette Machine without adhesive:
1. Feeding system: It consists of a quantitative feeding bin and a forced feeding deviceQuantitatively feeding bin used to feed briquette machine evenly and stably; Forced feeding device used to pressurize the materials and force it to the middle of the rollers
2. Transmission system: It is the power source and power transmission system of the briquette press.The main transmission system includes a motor, a reducer, a coupling, and a briquette groove alignment device, which are transmitted to the two roller shafts respectively.The main power supply adopts a speed-controlled motor, which is transmitted to the driving shaft through a pulley and a cylindrical gear reducer. The open gear is between the driven shaft and the non-driven shaft to ensure synchronous operation.
3. Forming system: It is the main device for pressing materials into briquettes. It consists of a pressing roller, a main shaft, a bearing and a bearing seat, and a synchronous gear.
4. Finished briquette screening and conveying device: briquette screening and cleaning device.And transported to the storage area by belt conveyor.
5. Hydraulic system:It consists of hydraulic pump and hydraulic cylinders and oil pipe.When there is too much feed or a metal block appears, the hydraulic cylinder piston rod is overloaded by pressure, the hydraulic pump will stop, the accumulator will buffer the pressure change, the overflow valve will open to return oil, and the piston rod will shift to increase the gap between the pressing rods, so that hard objects can pass through the pressing rods. Such a system design can protect the pressing rods from damage.
6. PLC control system: Intelligently controls the feeding and transmission devices of the briquette press.
Model | GY520 | GY650 | GY750 | GY850A | GY850B | GY1000A | GY1000B | GY1200 | GY1400 | |
Capacity (t/h) | 2.5-3.5 | 4-5 | 6-8 | 8-10 | 12-15 | 15-18 | 20-25 | 15-18 | 20-25 | |
Roller width(mm) | 196 | 200 | 225-300 | 350 | 500 | 350-500 | 500-650 | 900 | 1000 | |
Roller diameter(mm) | 522 | 650 | 750 | 850 | 850 | 1000 | 1000 | 1200 | 1400 | |
Main Motor Power | kW | 55-75 | 75-90 | 132-185 | 185-200 | 200-250 | 280 | 315 | 280×2 | 355×2 |
HP | 74.8-102 | 102-122.4 | 179.5-251.9 | 251.9-272 | 272-340 | 380.8 | 428.4 | 380.8×2 | 482.8×2 | |
Reducer | Single Drive/Dual Drive | Dual Drive | ||||||||
Hydraulic station power | kW | 3 | 3 | 3 | 3 | 4 | 4 | 4 | 5.5 | 5.5 |
HP | 4.08 | 4.08 | 4.08 | 4.08 | 5.44 | 5.44 | 5.44 | 7.48 | 7.48 | |
Preload Motor Power | kW | 18.5 | 18.5 | 22 | 30 | 30×2 | 45 | 37×2 | 45×2 | 45×2 |
HP | 25.16 | 25.16 | 29.92 | 40.8 | 40.8×2 | 61.2 | 50.32×2 | 61.2×2 | 61.2×2 | |
Maximum total pressure(t) | 240 | 300 | 450 | 630 | 1100 | 1100 | 1200 | 1200 | 1200 | |
Rate dline pressure(t/cm) | 10 | 12 | 15 | 18 | 20 | 20 | 20 | 12 | 10 |
Note:The above data is based on lime with a bulk density of 1.2. For specific materials, please refer to the parameters in the specific equipment quotation table.
FAQ's
Frequently Asked Questions
What products does your manufacturing company produce?
We provide a wide range of machinery, including briquette machines, mixers, dryers, and more, designed for various industrial applications.
What is the typical lead time for product delivery?
Lead times vary depending on the machine and customization options. Please contact us for specific timelines related to your order.
What materials can your briquette machines process?
Our briquette machines can process a variety of materials, including biomass, charcoal, and other organic waste products.
What are the energy requirements for your machines?
Each machine has specific energy requirements, which can be provided upon request. We aim to design energy-efficient solutions.
Request A Quote
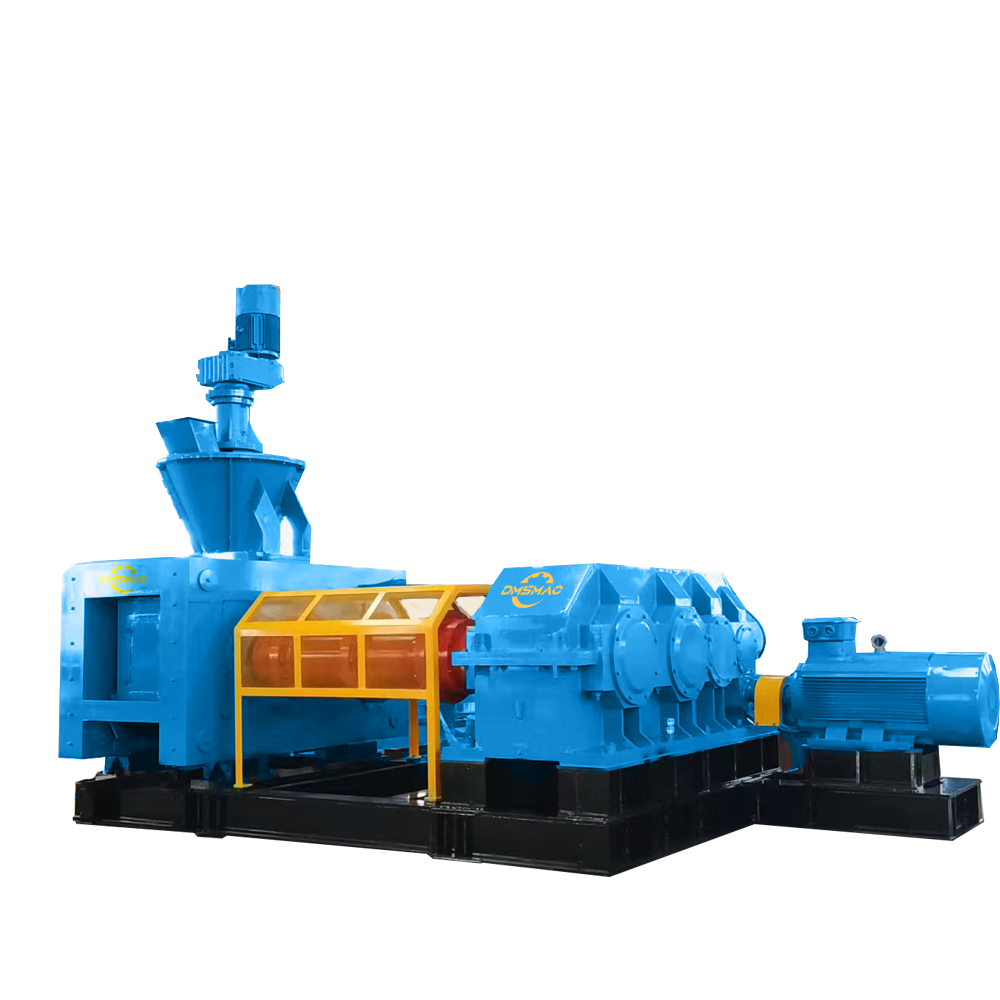
Briquette Machine Without Adhesives
Production Capacity: 1000-50000 kgs Per Hour
Application: Press materials into briquettes without adhesive and water by super high power, such as Coal, mining, metallurgy, refractory materials, chemical industry, building materials and other industries.
Briquette Shape and Size:Oval,Square,Pillow Shape & Customizable 15mm-100mm
Features:
- Stable speed, high molding rate, uniform briquette size;
- Higher, adjustable molding pressure for improved product quality.
- Safe, reliable molding system with easy-to-replace parts and low maintenance.
- The structure is simple and compact, saving space.
- Smooth demoulding, low noise and less dust;
- PDF DOWNLOAD
▶Fields of Application
You will find in this page, examples of industrial applications using our briquetting technology.
Of course this list is not exhaustive and we hope that you will not hesitate to contact us in order to obtain more technical information about ways to process your product:
–Chemicals (sodium sulphate, sodium chloride, sodium formate, maleic anhydride, carbonates, sodium cyanide, potassium cyanide, iron sulphate, potassium bromide, ammonium bromide, boric acid, urea, precipitated silica, dimethyl terephthalate, polymers …)
–Minerals (alumina, bauxite, lime, hydrated lime, burnt lime, dolomite, gypsum, china clay, magnesia, fluorspar, paint pigments, sulphur, fluorite, molybdenum oxide…)
–Gypsum from power station flue gas desulphurisation
–Fertilizers (potash)
–Minerals (aluminium, chromium, cobalt, copper, iron, iron ore, manganese, lead, zinc, nickel, hematite, lead ore…)
–Coal: production of briquettes for home or industrial heating (partial coke oven charge, briquettes treated to obtain formcoke, briquettes for gasification).
–Coal for production of activated carbon
–Lignite-brown coal, peat, etc…
–Charcoal
–By-products from steel mills and metallurgy
–Graphite, carbon black
–Clay, bentonite
–Detergents
–Steelworks waste materials and by-products (sludge, mill dust, sintering fines, mill scale, coke fines, flue dust…)
–Dried sewage sludge
–Silicon
–Aromatic powder
–Sugar
…
▶Product Advantage:
—With Hydraulic System,Effectively Extend The Service Life of the Roller
—Horizontal and Vertical Feed for Screw or Gravity Feed Options
—Pocket Adjustment Design to Make Sure Getting Beautiful Final Briquettes
—Customized Sizes and Shapes for Briquettes
—Variable Speed Roll and Screw Feeder Drives to Maximize Product Quality
—Rolls and Feed Screws Available In Wear and Corrosion-Resistant Alloys
—Designed For Easy Maintenance
▶Working Principle:
The briquetting process allows the compression of volatile or voluminous powders between two rollers rotating in opposite directions in order to obtain a calibrated shape and size with higher densification. This densification step offers many possibilities regarding the use of the material and, in some cases, it can also be an essential condition for the continuation of the process.
Model | GY520 | GY650 | GY750 | GY850A | GY850B | GY1000A | GY1000B | GY1200 | GY1400 | |
Capacity (t/h) | 2.5-3.5 | 4-5 | 6-8 | 8-10 | 12-15 | 15-18 | 20-25 | 15-18 | 20-25 | |
Roller width(mm) | 196 | 200 | 225-300 | 350 | 500 | 350-500 | 500-650 | 900 | 1000 | |
Roller diameter(mm) | 522 | 650 | 750 | 850 | 850 | 1000 | 1000 | 1200 | 1400 | |
Main Motor Power | kW | 55-75 | 75-90 | 132-185 | 185-200 | 200-250 | 280 | 315 | 280×2 | 355×2 |
HP | 74.8-102 | 102-122.4 | 179.5-251.9 | 251.9-272 | 272-340 | 380.8 | 428.4 | 380.8×2 | 482.8×2 | |
Reducer | Single Drive/Dual Drive | Dual Drive | ||||||||
Hydraulic station power | kW | 3 | 3 | 3 | 3 | 4 | 4 | 4 | 5.5 | 5.5 |
HP | 4.08 | 4.08 | 4.08 | 4.08 | 5.44 | 5.44 | 5.44 | 7.48 | 7.48 | |
Preload Motor Power | kW | 18.5 | 18.5 | 22 | 30 | 30×2 | 45 | 37×2 | 45×2 | 45×2 |
HP | 25.16 | 25.16 | 29.92 | 40.8 | 40.8×2 | 61.2 | 50.32×2 | 61.2×2 | 61.2×2 | |
Maximum total pressure(t) | 240 | 300 | 450 | 630 | 1100 | 1100 | 1200 | 1200 | 1200 | |
Rate dline pressure(t/cm) | 10 | 12 | 15 | 18 | 20 | 20 | 20 | 12 | 10 |
Note:The above data is based on lime with a bulk density of 1.2. For specific materials, please refer to the parameters in the specific equipment quotation table.