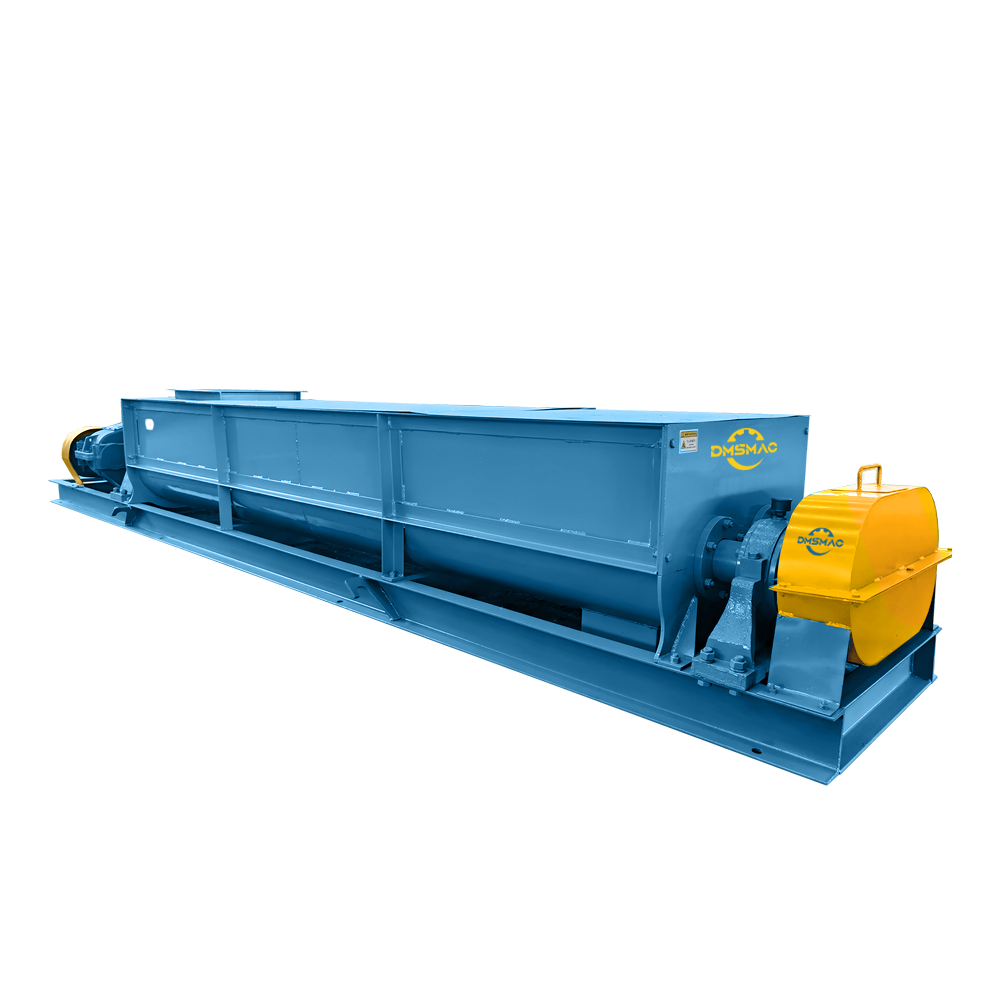
Double Shaft Mixer-Continuous Type
Production: 0.5-50 tons/hour
Application: Continuous production of heavy and sticky and wet materials, such as: coal briquette production line mixing work, charcoal briquettes production line mixing work, clay brick production line, etc.;
Features:
- Continuous production line, realizing large-scale continuous mixing work;
- High Mixing Efficiency, through shearing, impact, multi-directional repeated stirring, to achieve uniform mixing effect;
- Powerful, suitable for mixing a variety of heavy, sticky and wet materials;
- Simple and Stable Structure, using double-shaft synchronous reverse rotation, while taking into account the mixing, can convey materials;
- Spraying device or steam heating humidification device can be installed as needed.
- PDF DOWNLOAD
The double-shaft mixer is a device that achieves material mixing, homogenization or humidification through the coordinated rotation of two stirring shafts. Its working principle combines mechanical movement with the dynamic characteristics of materials. It has a reasonable design, efficient and stable operation, and good stirring effect. It is widely used in the briquetting production line.
1. Composition of twin-shaft mixer:
1-1: Motor, power output device;
1-2: Reducer, converts the high speed of the motor into low speed and high torque, and transmits it to the mixing shaft;
1-3: Gearbox: The gears installed synchronously in reverse are connected to the two main shafts;
1-4: Mixing blades: Driven by the main shaft, synchronous reverse operation provides shearing, impacting and flipping, and pushes the material forward to achieve shear mixing, convection mixing, and diffusion mixing;
1-5: Box and frame and cover: Provide storage and mixing space for materials, and the added cover helps to prevent dust from spilling;
2. Core structure and movement mode of twin-shaft mixer:
2-1: Twin-shaft structure: Two parallel mixing shafts achieve synchronous rotation through synchronous reverse rotating gear transmission, so that the material is fully sheared, impacted and flipped by the blades between the two shafts;
2-2: Distribution of mixing blades: Spiral fan-shaped blades, blades or mixing arms are installed on the shaft, staggered at a certain angle to form a continuous propulsion and mixing effect. The shape of the blades can be adjusted according to the characteristics of the material (such as wide blades for viscous materials and narrow blades for loose materials).
3. Working principle of the twin-shaft mixer:
3-1: Shear mixing
When rotating in opposite directions, the two-shaft blades exert shear force on the material, tearing the agglomerated materials and destroying the material stratification, which is suitable for the dispersion and homogenization of powdery or viscous materials (such as anthracite). When rotating at differential speeds, the high and low speed blades form a velocity gradient to enhance the local shear effect.
3-2: Convection mixing
The mixing blades push the material to move in the axial and radial directions, forming a three-dimensional circulation flow, promoting the exchange of materials in different regions (such as the uniform distribution of anthracite, adhesives and water). When rotating in the same direction, the material flows in the same direction, which is suitable for continuous production lines (such as briquette production).
3-3: Diffusion mixing
At the microscopic level, the material particles produce Brownian motion due to mechanical vibration and collision, achieving fine homogenization.
4. Materials moving direction
4-1: Feeding stage
The material and the adhesive to be added enter the mixing chamber through the feed port, and the double-axis mixing blades quickly disperse them throughout the chamber.
4-2: Mixing stage
The material is repeatedly sheared, impacted, and flipped under the action of the mixing blades, and is pushed along the axial direction to gradually achieve homogenization.
If humidification is required (such as coal powder humidification), the spray system will simultaneously inject water, and the mixing blades will rotate to fully wet the liquid, solid and additives.
4-3: Discharging stage
The mixed material is pushed to the discharge port for discharge. Some models use bottom door or spiral conveying structure to ensure continuous operation.
Model | Barrel Dia.
(mm) |
Capacity
(kg) |
Spindle Speed (r/min) | Power
(kw) |
Capacity
(t/h) |
S110 | 1000 | 110 | 44 | 5.5 | 1-1.3 |
S112 | 1450 | 200 | 34.7 | 7.5 | 2.2-2.5 |
S114 | 1800 | 300-400 | 34 | 15 | 4-6 |
S118 | 1850 | 500 | 33 | 22 | 5-8 |
S1120 | 2000 | 1000 | 25 | 30 | 8-10 |
S1124 | 2400 | 1500 | 20 | 37 | 13-15 |
FAQ's
Frequently Asked Questions
What products does your manufacturing company produce?
We provide a wide range of machinery, including briquette machines, mixers, dryers, and more, designed for various industrial applications.
What is the typical lead time for product delivery?
Lead times vary depending on the machine and customization options. Please contact us for specific timelines related to your order.
What materials can your briquette machines process?
Our briquette machines can process a variety of materials, including biomass, charcoal, and other organic waste products.
What are the energy requirements for your machines?
Each machine has specific energy requirements, which can be provided upon request. We aim to design energy-efficient solutions.
Request A Quote
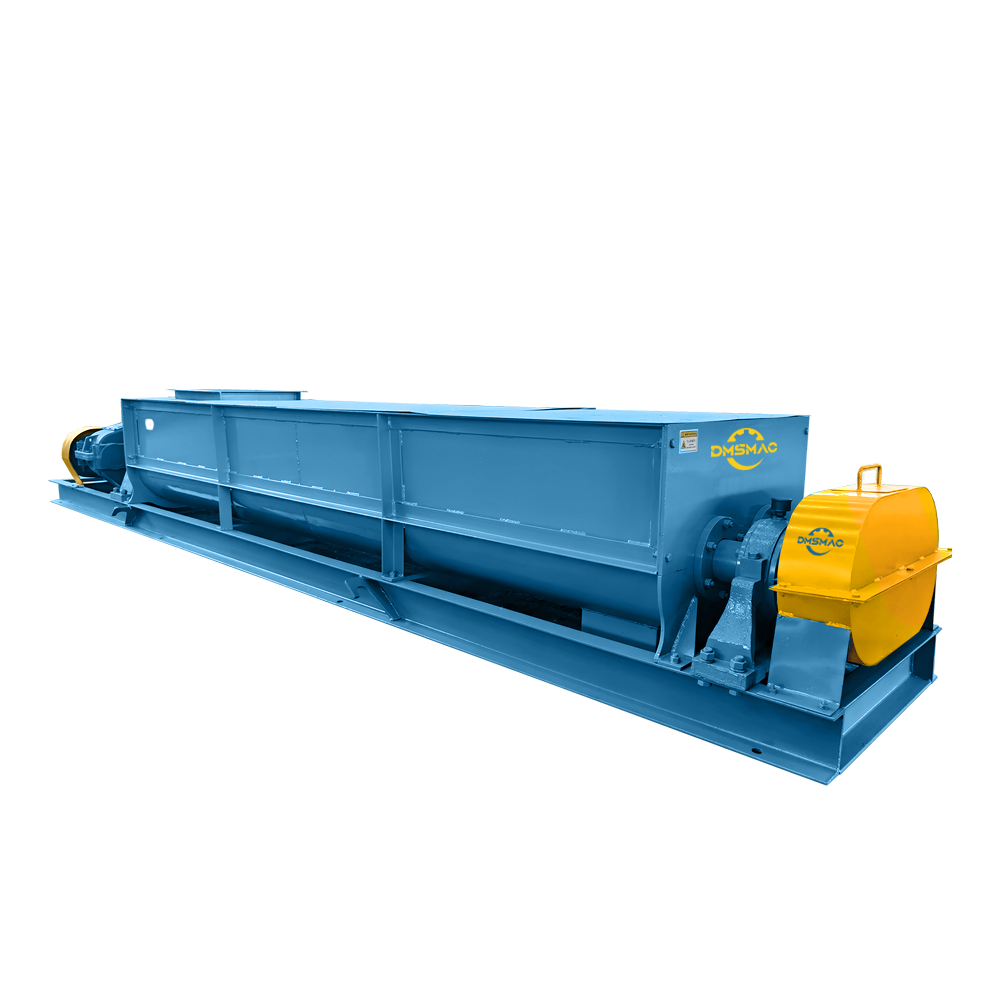
Double Shaft Mixer-Continuous Type
Production: 0.5-50 tons/hour
Application: Continuous production of heavy and sticky and wet materials, such as: coal briquette production line mixing work, charcoal briquettes production line mixing work, clay brick production line, etc.;
Features:
- Continuous production line, realizing large-scale continuous mixing work;
- High Mixing Efficiency, through shearing, impact, multi-directional repeated stirring, to achieve uniform mixing effect;
- Powerful, suitable for mixing a variety of heavy, sticky and wet materials;
- Simple and Stable Structure, using double-shaft synchronous reverse rotation, while taking into account the mixing, can convey materials;
- Spraying device or steam heating humidification device can be installed as needed.
- PDF DOWNLOAD
Application
Wheel grinding mixer, apply to mixing solid material and liquid amterial in any production line, such as casting plant, coal briquettes plant, charcoal briquettes plant, brick plant and so on, widely applied in various kinds of forming production line. It is a kind of ideal mixing equipment can be easily used in chemical industry, light industry, building materials, and other industries mixing with powder materials. The heavy duty rollers can grind the materials, meanwhile, heavy rolls will give much pressure to the materials to extend the bulk density of materials, greatly support for next briquettes pressing process. Widely work with quantitative feeding device and double shaft mxier to get automatic briquetting production line.
Working Pinciple
The motor pass the power to gear box, and vertical shaft will drive the two rotary rollers and blade. The blade will continuously lifts and stirs the material, and heavy pressing roller compacts the mixed material again. During the stirring and compacting again and again, the mixed material is fully stirred. Due to pressing roller further pressing during mixing, the bulk density of the material is further improved.
Engineering Case
Model | Barrel Dia.
(mm) |
Capacity
(kg) |
Spindle Speed (r/min) | Power
(kw) |
Capacity
(t/h) |
S110 | 1000 | 110 | 44 | 5.5 | 1-1.3 |
S112 | 1450 | 200 | 34.7 | 7.5 | 2.2-2.5 |
S114 | 1800 | 300-400 | 34 | 15 | 4-6 |
S118 | 1850 | 500 | 33 | 22 | 5-8 |
S1120 | 2000 | 1000 | 25 | 30 | 8-10 |
S1124 | 2400 | 1500 | 20 | 37 | 13-15 |