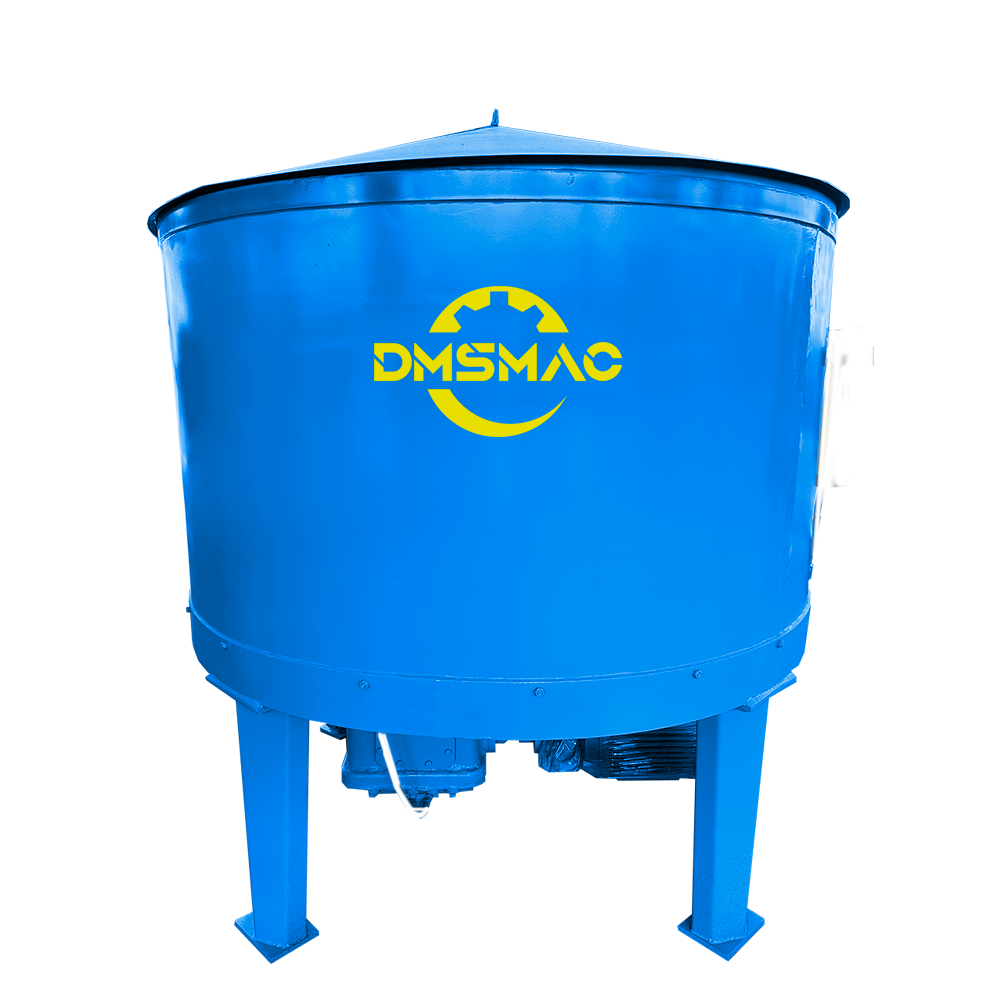
Wheel Grinding Mixer
Processing Capacity: 0.1-1 cubic meters/time;
Applicable materials: Mainly suitable for batch processing of materials with poor bulk density, poor water absorption, or wet materials, sticky materials, and semi-dry hard materials, which can increase density and evenly mix.
Features:
- Increase the Bulk Density of Materials: increase the pressure on the materials during the mixing process and reduce the gap between the materials;
- Accurately control the rate of materials added: work with the weighing device to accurately control the proportion of added materials;
- Accurately control the mixing time: the unloading time can be automatically controlled by PLC;
- Wide range of applications: It can be applied to dry materials, wet materials, soft materials, hard materials and sticky materials;
- Sturdy and durable, long life, simple maintenance: cast wear-resistant pressure wheels and wear-resistant boxes to ensure quality.
- PDF DOWNLOAD
The wheel mill mixer (also known as the planetary mixer also) is a mechanical equipment that combines rolling and mixing functions. It is mainly used to mix wet, sticky or semi-dry hard materials with low density and poor water absorption. It increases the bulk density of the materials during the mixing process and plays a role in uniform mixing through continuous flipping and compaction. Its core function is to achieve strong kneading, rolling, crushing and mixing of materials through the gravity of the roller and the flipping and shearing action of the mixing blades. It is widely used in coal production lines, carbon black briquette production lines, charcoal briquettes production lines and some mineral powder briquette production lines, etc.
1. Working principle and working process of wheel mill mixer:
The wheel mill mixer homogenizes the materials through the compound action of repeated turning, press, shearing and kneading. The specific process is as follows:
1-1: Roller rotation drive
The motor drives the roller to rotate clockwise or counterclockwise around the vertical axis through the reducer. The roller rolls passively on the roller plate due to friction, and at the same time, the roller exerts vertical pressure on the material under the action of gravity;
1-2: Pre-pressing and crushing
Rolling action: The solid cast roller squeezes the material with a pressure of hundreds to thousands of Newtons, destroying the agglomeration of particles (such as agglomerated coal powder or carbon black blocks), and under the action of binder and water, discharges the air in the material and increases the bulk density of the material.
Crushing action: The solid roller forms a relative motion with the roller plate when rolling, generating a lateral shear force, further refining the particles and promoting the mixing of water and binder with the material.
1-3: Mixing and turning
Scraper/mixing blade: The scraper rotating with the main shaft pushes the edge material to the center, and at the same time turns up the material from the bottom, and is rolled again by the roller. After repeated turning and rolling, the uniformity of the material is effectively guaranteed.
Convection mixing: The material diffuses outward under the centrifugal force of the rotating roller, and is forced back by the roller and scraper to form a circular flow.
1-4: Humidity adjustment
If humidification is required (such as carbon powder molding, carbon black molding), water is injected into the roller through the spray system, and the roller rolls to make the water evenly penetrate into the material.
1-5: Discharging
After mixing is completed, stop the roller from rotating, open the bottom discharge door, and the material is discharged with the help of the scraper.
2. Technical advantages:
1. Increase the packing density of materials: Increase the pressure on the materials during the mixing process (adjustable pressure), combine rolling (vertical pressure) with mixing (horizontal shear), continuously lift, squeeze, knead, expel the air in the materials, and reduce the gaps between the materials; increase the packing density of materials and effectively improve the quality of finished pellets; widely used in the mixing process of low-density, poor water absorption, high moisture, high viscosity, and easy-to-agglomerate materials;
2. Accurately control the amount of various materials added: Use weighing devices to accurately control the proportion of added materials and save the consumption of additives;
3. Accurately control the mixing speed and mixing time: The mixing speed and unloading time can be automatically controlled by PLC to meet different process requirements;
4. Wide range of applications: It can be applied to low-density, high-moisture, poor water absorption, high viscosity, easy-to-agglomerate dry materials, wet materials, soft materials, hard materials and other materials;
5. Sturdy and durable, long life, simple maintenance: cast reducer housing and wear-resistant pressure wheel, and wear-resistant box body guarantee quality.
FAQ's
Frequently Asked Questions
What products does your manufacturing company produce?
We provide a wide range of machinery, including briquette machines, mixers, dryers, and more, designed for various industrial applications.
What is the typical lead time for product delivery?
Lead times vary depending on the machine and customization options. Please contact us for specific timelines related to your order.
What materials can your briquette machines process?
Our briquette machines can process a variety of materials, including biomass, charcoal, and other organic waste products.
What are the energy requirements for your machines?
Each machine has specific energy requirements, which can be provided upon request. We aim to design energy-efficient solutions.
Request A Quote
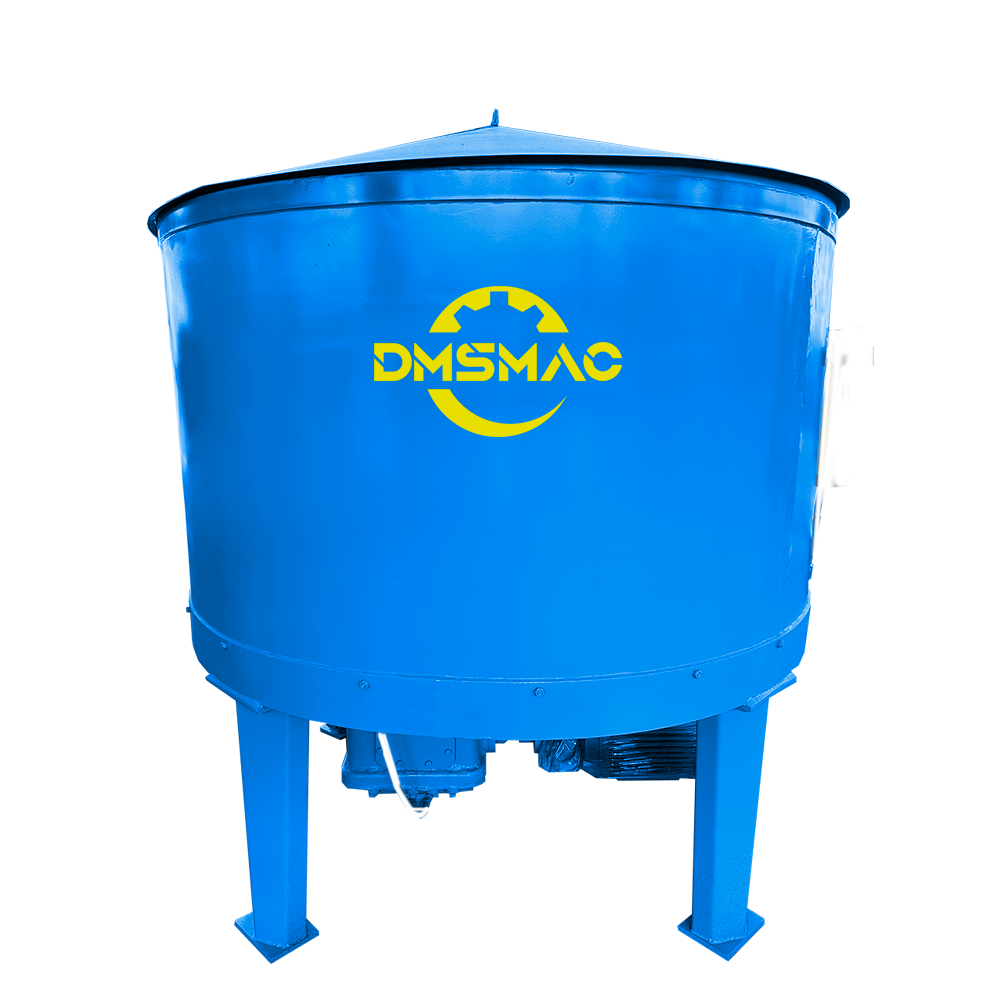
Wheel Grinding Mixer
Processing Capacity: 0.1-1 cubic meters/time;
Applicable materials: Mainly suitable for batch processing of materials with poor bulk density, poor water absorption, or wet materials, sticky materials, and semi-dry hard materials, which can increase density and evenly mix.
Features:
- Increase the Bulk Density of Materials: increase the pressure on the materials during the mixing process and reduce the gap between the materials;
- Accurately control the rate of materials added: work with the weighing device to accurately control the proportion of added materials;
- Accurately control the mixing time: the unloading time can be automatically controlled by PLC;
- Wide range of applications: It can be applied to dry materials, wet materials, soft materials, hard materials and sticky materials;
- Sturdy and durable, long life, simple maintenance: cast wear-resistant pressure wheels and wear-resistant boxes to ensure quality.
- PDF DOWNLOAD
Double Shaft Mixer
Double shaft mixer is used in coal processing or brick making industry. Its maintenance is simple, stable,high efficiency and energy saving. It adopts double shaft propeller crossing type, in the process, cutting, pulling and stirring atone time to make material fully be mixed. Propeller angle can be adjusted to tally with required evenness. Due to it’s continuous working performance, it is more suitable for line production.
Working Principle
The double shaft is driven by motor and gear box through gear, the blade with angle is driven following shaft circular motion. The materails are lifted to move forward following the blade rotary moving. The blade angle can be set as request to set the mixing time and speed. Normally, many sets mixer will be set together to work to guarantee the mixing time and quality.
Technical Data
Model | Capacity
(t/h) |
Chute length
(mm) |
Propeller Diameter
(mm) |
Power
(kw) |
Stirring type | Spraying type |
ZZDM3000 | 7-10 | 3-4 | 350 | 11-15 | Double shaft propeller stirring | Straight +Spraying Nozzole |
ZZDM4000 | 10-18 | 3-4 | 450 | 15-22 | ||
ZZDM5000 | 15-25 | 3-5 | 550 | 22-37 | ||
ZZDM6000 | 22-32 | 3-5 | 650 | 37-45 | ||
Remarks | Capacity will be different based on various material specific gravity. above capacity based on industry coal fines. |
Advantage of Double Shaft Mixer
1, Sturdy and durable due to the steel alloy balde and solid axle
2, Continuous working by 7*24h
3, Speed regular as output request
4, Powerful enough for large output as request, gear box and motor driven system
5, Dust free due to the cover assembled
6, Can be heating by steam at special cold area