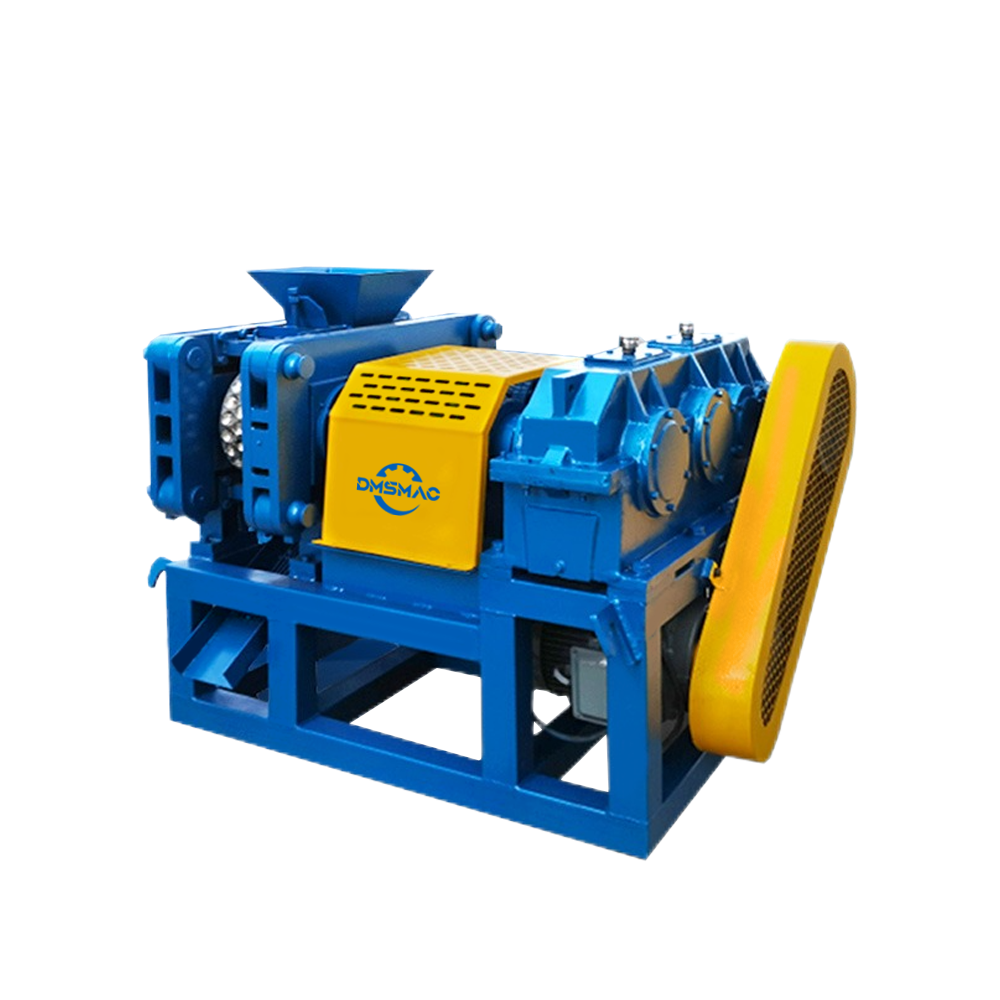
Laboratory Briquette Machine/Compactor
FEATURES
1: Cantilevered roll design for easy roll replacement;
2: Pockets are available in different shapes and sizes;
3: Vacuum de-aeration available for fine powder applications;
4: Variable speed roll and screw feeder drives to maximize product quality;
5: Rolls and feed screws are available in wear and corrosion resistant alloys;
6: Rugged industrial frame construction;
7: Heavy duty long lasting bearings and drive components;
8: Designed for ease of maintenance;
- PDF DOWNLOAD
DMSMAC developped a range of lab briquette machine/compactors for research and small laboratory projects,which can provide conclusive briquetting (compaction) tests on a variety of materials with samples.
This equipment enables to make briquetting and compaction-granulation feasibility studies on a wide variety of products in very small quantities (about one liter for one test, a few dozen kg/h in continuous use).
Another advantage of this equipment is that the pieces in contact with the product can be easily and rapidly dismantled, cleaned and reassembled. These pieces can be handled without any particular tools.
According to its configuration, the lab briquette machine/compactor produces:
- either briquettes in varied shapes (pillow, soap, stick,…) and volume from 0,5 cm3 to about 5 cm3.
- or granules from 500 µm to 5 mm.
FEEDING SYSTEM OF THE LAB BRIQUETTE MACHINE/COMPACTOR
The laboratory briquette machine/compactor is equipped with a forced feeder with a conical screw for feeding the rollers. Due to its conical shape, the forced feeder is able to pre-compact the powder before compaction, resulting in a better compacted product. For highly aerated and low-density powders, an optional degassing device (vacuum pump) can be installed in the forced feeder to remove the air contained in the product before compaction.
ROLLERS
The rollers are mounted in a cantilevered manner, or external to the mechanical part of the machine. This special design allows the “processing area” to be completely isolated from the mechanical part of the laboratory compactor.
The surface of the rollers (pocketed, knurled, corrugated, etc.) depends on the raw material characteristics and the desired end product.
HYDRAULIC SYSTEM
The hydraulic system allows the force on the moving roller to be adjusted to the product.
GRANULATOR
Regarding the compaction granulation process, the micro compactor is equipped with a granulator, whose rotor and screen are also cantilever mounted to isolate the “processing area” from the mechanical part.
To improve efficiency and meet the requirements of small particle size, a secondary granulator can be installed directly below the first granulator.
CONTROL PANEL
The laboratory briquette machine is equipped with a control and drive panel that allows adjustment and display of different operating parameters (screw speed of the forced feeder, rollers speed, pressure in the hydraulic circuit, rotor speed of the granulator) and continuous checking of operating conditions (motor current, product charge…)
OPTIONS
The laboratory briquette machine/compactor can be customized with the following available options:
- Parts in contact with the product in 304L or 316L stainless steel.
- All parts in 304L or 316L stainless steel.
- Double granulator.
- Degasser system for forced feeder, possibly with cheek plates.
- Roller cooling system.
- Flake sampling device before granulation.
- Control/drive system with data logging
- Force sensor
FEATURES/HIGHLIGHTS
- Cantilevered roll design for easy roll replacement
- Pockets are available in different shapes and sizes
- Vacuum de-aeration available for fine powder applications
- Variable speed roll and screw feeder drives to maximize product quality
- Rolls and feed screws are available in wear and corrosion resistant alloys
- Rugged industrial frame construction
- Heavy duty long lasting bearings and drive components
- Designed for ease of maintenance
GYC100 | GYC200 | |
Rolls diameter (mm) | 100 | 200 |
Rolls width (mm) | 30 | 75 |
Max system pressure (Mpa) | 20 | 25 |
Rolls surface pressure (Ton) | 7 | 25 |
Rolls speed (Rpm) | 0 – 25 | 0 – 25 |
Force-feeder speed (Rpm) | 0 – 150 | 0 – 150 |
Total power (Kw) | 3 | 11.95 |
Dimension (mm) | 850x820x1352 | 1350x1450x2455 |
Weight (kg) | 500 | 2000 |
FAQ's
Frequently Asked Questions
What products does your manufacturing company produce?
We provide a wide range of machinery, including briquette machines, mixers, dryers, and more, designed for various industrial applications.
What is the typical lead time for product delivery?
Lead times vary depending on the machine and customization options. Please contact us for specific timelines related to your order.
What materials can your briquette machines process?
Our briquette machines can process a variety of materials, including biomass, charcoal, and other organic waste products.
What are the energy requirements for your machines?
Each machine has specific energy requirements, which can be provided upon request. We aim to design energy-efficient solutions.
Request A Quote
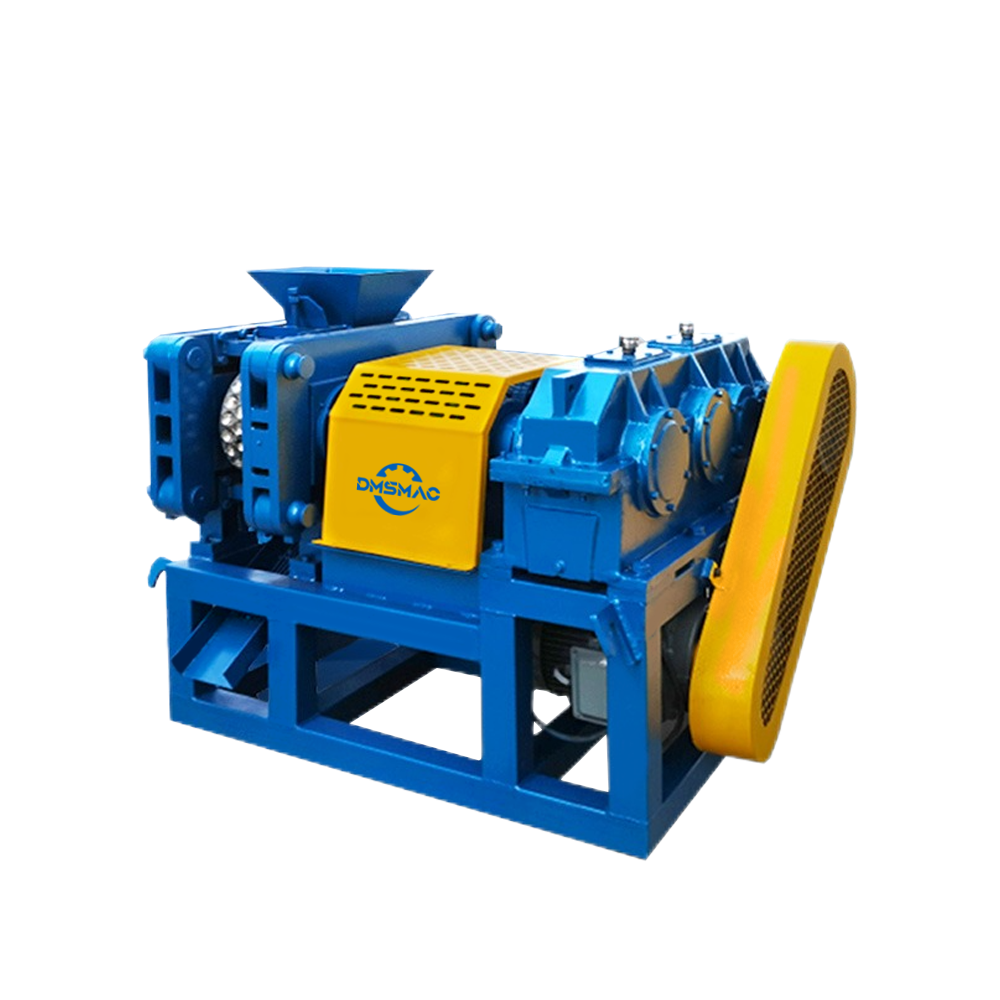
Laboratory Briquette Machine/Compactor
FEATURES
1: Cantilevered roll design for easy roll replacement;
2: Pockets are available in different shapes and sizes;
3: Vacuum de-aeration available for fine powder applications;
4: Variable speed roll and screw feeder drives to maximize product quality;
5: Rolls and feed screws are available in wear and corrosion resistant alloys;
6: Rugged industrial frame construction;
7: Heavy duty long lasting bearings and drive components;
8: Designed for ease of maintenance;
- PDF DOWNLOAD
▶Fields of Application
You will find in this page, examples of industrial applications using our briquetting technology.
Of course this list is not exhaustive and we hope that you will not hesitate to contact us in order to obtain more technical information about ways to process your product:
–Chemicals (sodium sulphate, sodium chloride, sodium formate, maleic anhydride, carbonates, sodium cyanide, potassium cyanide, iron sulphate, potassium bromide, ammonium bromide, boric acid, urea, precipitated silica, dimethyl terephthalate, polymers …)
–Minerals (alumina, bauxite, lime, hydrated lime, burnt lime, dolomite, gypsum, china clay, magnesia, fluorspar, paint pigments, sulphur, fluorite, molybdenum oxide…)
–Gypsum from power station flue gas desulphurisation
–Fertilizers (potash)
–Minerals (aluminium, chromium, cobalt, copper, iron, iron ore, manganese, lead, zinc, nickel, hematite, lead ore…)
–Coal: production of briquettes for home or industrial heating (partial coke oven charge, briquettes treated to obtain formcoke, briquettes for gasification).
–Coal for production of activated carbon
–Lignite-brown coal, peat, etc…
–Charcoal
–By-products from steel mills and metallurgy
–Graphite, carbon black
–Clay, bentonite
–Detergents
–Steelworks waste materials and by-products (sludge, mill dust, sintering fines, mill scale, coke fines, flue dust…)
–Dried sewage sludge
–Silicon
–Aromatic powder
–Sugar
…
▶Product Advantage:
—With Hydraulic System,Effectively Extend The Service Life of the Roller
—Horizontal and Vertical Feed for Screw or Gravity Feed Options
—Pocket Adjustment Design to Make Sure Getting Beautiful Final Briquettes
—Customized Sizes and Shapes for Briquettes
—Variable Speed Roll and Screw Feeder Drives to Maximize Product Quality
—Rolls and Feed Screws Available In Wear and Corrosion-Resistant Alloys
—Designed For Easy Maintenance
▶Working Principle:
The briquetting process allows the compression of volatile or voluminous powders between two rollers rotating in opposite directions in order to obtain a calibrated shape and size with higher densification. This densification step offers many possibilities regarding the use of the material and, in some cases, it can also be an essential condition for the continuation of the process.
GYC100 | GYC200 | |
Rolls diameter (mm) | 100 | 200 |
Rolls width (mm) | 30 | 75 |
Max system pressure (Mpa) | 20 | 25 |
Rolls surface pressure (Ton) | 7 | 25 |
Rolls speed (Rpm) | 0 – 25 | 0 – 25 |
Force-feeder speed (Rpm) | 0 – 150 | 0 – 150 |
Total power (Kw) | 3 | 11.95 |
Dimension (mm) | 850x820x1352 | 1350x1450x2455 |
Weight (kg) | 500 | 2000 |