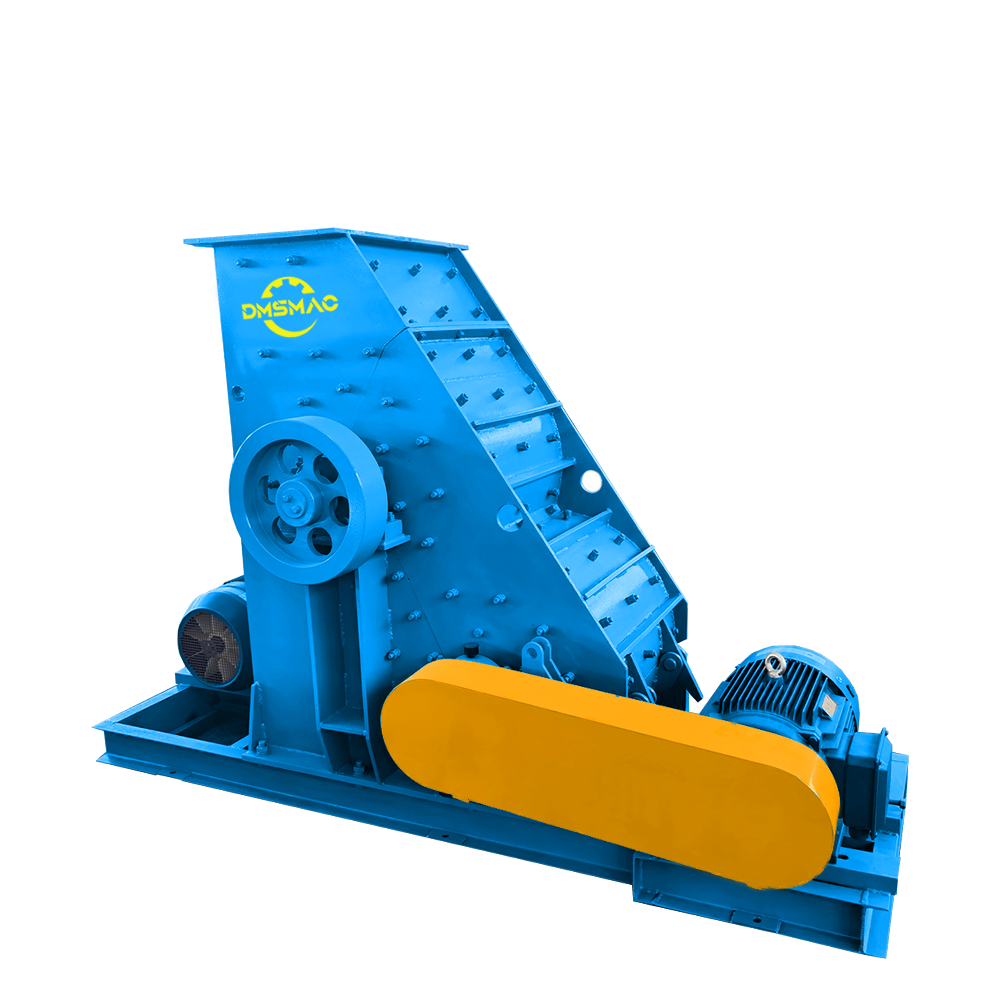
Double Stage Crusher
Processing Capacity: 10-100 tons/hour;
Application: Crushing equipment specially R&D for high-moisture materials such as anthracite, coal gangue, lignite and wet and sticky construction waste, widely used in different coal briquette production lines.
Features:
- No screen bottom anti-blocking design, specially used for crushing materials such as anthracite and coal gangue;
- Final dust≤3mm, Large feed particle size, small discharge particle size, and crushing ratio up to 30-50;
- Low energy consumption, compared with the same output and particle size discharge, energy consumption is reduced by about 25%;
- Reasonable structure, hydraulic opening of the box, simple maintenance and low cost;
- PDF DOWNLOAD
What is a double-stage crusher?
The double-stage crusher,the based on the traditional horizontal hammer crusher, is a crushing equipment with a double-rotor series structure, which achieves material refinement through two-stage continuous crushing. Its core components include upper and lower independent rotors, high alloy wear-resistant hammers and screen-free crushing chamber design, which are suitable for the treatment of medium and high hardness materials and highly wet and sticky waste materials.
How does a two-stage crusher work?
Primary Crushing: After the material enters the upper crushing chamber, the hammers of the first set of rotors rotate at high speed to perform strong impact and shearing to complete the coarse crushing.
Secondary Grinding: The coarsely crushed material is thrown into the lower crushing chamber, hit again by the second set of rotor hammers, and collides with the impact liner and self-friction between materials, forming a composite crushing effect of “hammer powder + material powder”.
Particle size control: The discharge particle size is adjusted by adjusting the rotor speed or the hammer gap, and uniform particles (usually ≤3mm) can be achieved without a screen.
What are the advantages of a two-stage crusher?
Screen-free anti-blocking design: It is suitable for materials with high moisture content (unlimited) such as coal gangue and wet and sticky construction waste to avoid blockage and shutdown.
Wear resistance and economy: The hammer head adopts shifting gap adjustment technology, which can be adjusted and reused after wear, and the service life is extended by 3 times; the combined hammer head structure only needs to replace the worn parts, reducing maintenance costs.
High efficiency and energy saving: The two-stage crushing process reduces unit energy consumption by 25%, the production capacity reaches 15-100 tons/hour (depending on the model), and the crushing ratio is as high as 30-50.
Environmental protection and low noise: The closed structure is combined with a dust removal device, and the dust emission is reduced by more than 60%, and the operating noise is ≤85dB
What are the technical parameters of the double-stage crusher?
Note:
The selection of crushing equipment needs to be accurately selected according to the hardness and particle size of the raw materials, the particle size and output of the output, and the moisture content of the materials. Please consult the engineer in detail to obtain an accurate quotation.
FAQ's
Frequently Asked Questions
What products does your manufacturing company produce?
We provide a wide range of machinery, including briquette machines, mixers, dryers, and more, designed for various industrial applications.
What is the typical lead time for product delivery?
Lead times vary depending on the machine and customization options. Please contact us for specific timelines related to your order.
What materials can your briquette machines process?
Our briquette machines can process a variety of materials, including biomass, charcoal, and other organic waste products.
What are the energy requirements for your machines?
Each machine has specific energy requirements, which can be provided upon request. We aim to design energy-efficient solutions.
Request A Quote
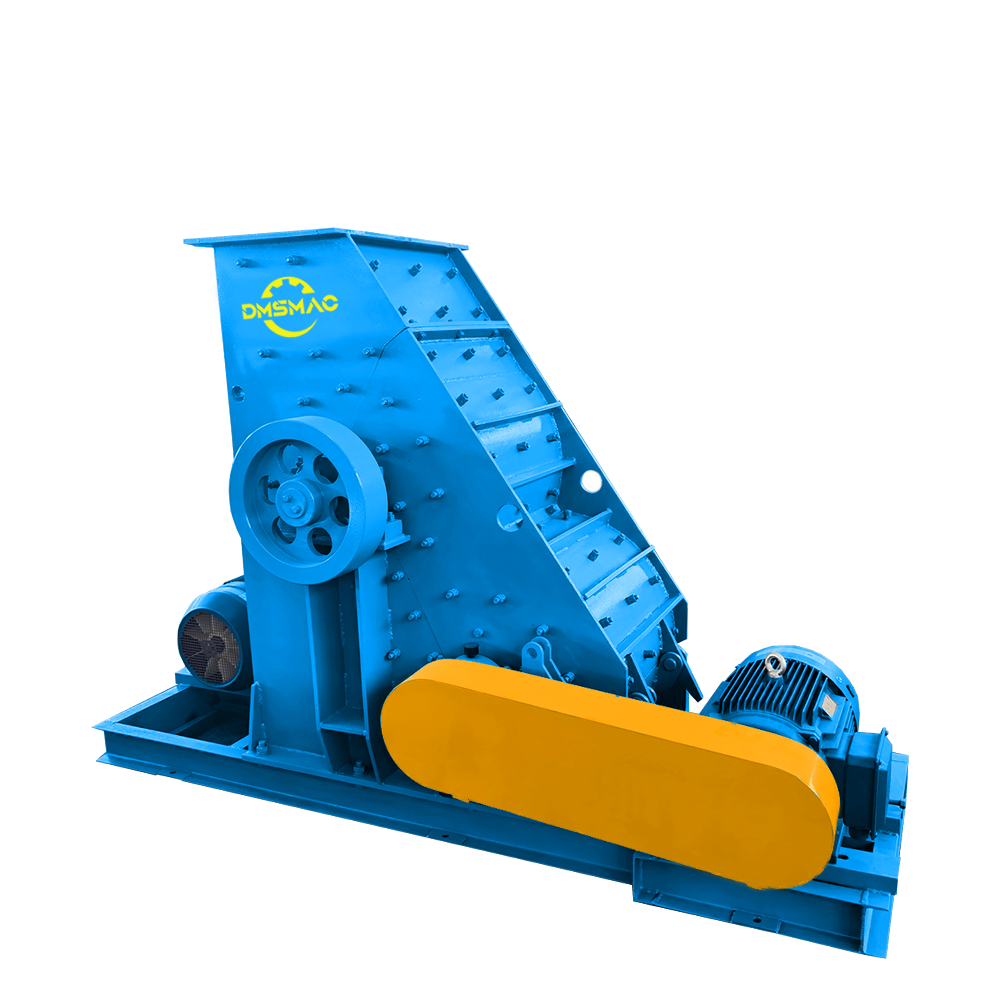
Double Stage Crusher
Processing Capacity: 10-100 tons/hour;
Application: Crushing equipment specially R&D for high-moisture materials such as anthracite, coal gangue, lignite and wet and sticky construction waste, widely used in different coal briquette production lines.
Features:
- No screen bottom anti-blocking design, specially used for crushing materials such as anthracite and coal gangue;
- Final dust≤3mm, Large feed particle size, small discharge particle size, and crushing ratio up to 30-50;
- Low energy consumption, compared with the same output and particle size discharge, energy consumption is reduced by about 25%;
- Reasonable structure, hydraulic opening of the box, simple maintenance and low cost;
- PDF DOWNLOAD