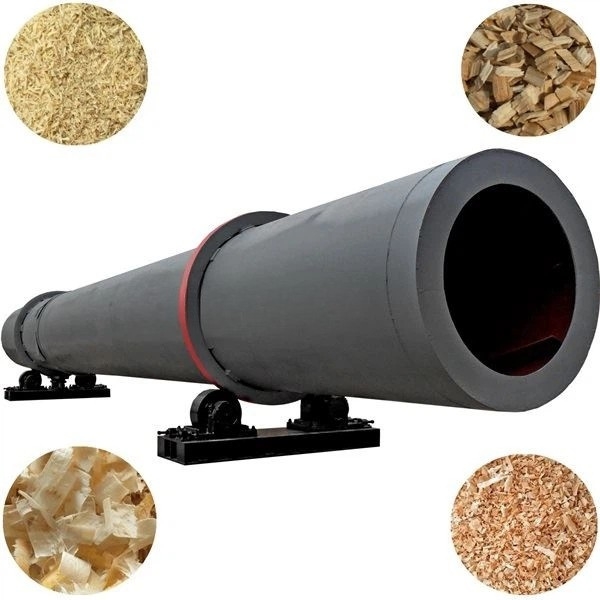
Drum Dryer
Drying moisture: from 60% to 1% of raw materials;
Output: 300 kg/hour-50,000 kg/hour
Applicable raw materials: mainly for drying powdered/granular materials with good fluidity, such as coal slime, sawdust, slag, mineral powder dust removal ash, etc.
Features:
- High dehydration efficiency: The rotary drum design allows the hot air flow to directly contact the surface of the material, combined with the rotation of the drum to achieve continuous tumbling and throwing of the material, greatly improving the heat exchange efficiency and shortening the drying time;
- Continuous 24h/30d operation, huge processing capacity: The rotary drum dryer adopts continuous operation to meet the needs of scale;
- Low energy consumption and wide practicality of heat source: It can accept different heat sources for heating or heat exchange, such as various biomass materials, coal, oil, gas, etc.;
- PLC automatic control: visible operation, checkable data, high degree of automation;
- Low operation and maintenance cost: The equipment is reasonably designed, simple in structure, and low in operation and maintenance costs.
- PDF DOWNLOAD
1. What is rotary drum dryer?
The rotary drum dryer is named because of its appearance and operation mode. It is a contact-type downstream heat conduction continuous drying equipment. The material is lifted by the rotation of the drum to achieve direct contact between the hot air and the material, thereby achieving the purpose of drying the material. According to the characteristics of the raw materials and the production requirements, the drum can be designed into three layers, also known as a three-pass dryer.
2. What materials can be dried by rotary drum dryer?
Drum dryers are widely used in various granular and powdery materials, and the materials require a certain fluidity. For example: coal slime, lignite, anthracite, as well as sawdust, lees, slag and other materials. Design the corresponding drum dryer according to the following customer information:
-Raw material name and particle size?
-Raw material moisture content before drying?
-Finished product moisture content requirements after drying?
-Required processing volume?
-Fuel selection?
-Others: environmental protection requirements, installation dimensions, and temperature change range of the working environment, etc.
3. What is the structure and composition of the rotary drum dryer?
The rotary drum dryer consists of the following parts:Â
Heat source system;Â
Drying body drum;Â
Drive device;Â
Dust removal system;Â
Electronic control system;
Other components;
3-1. Heat source system
The heat source system includes the combustion system (hand-fired hot air stove, continuous stove, biomass stove, gas hot air stove, etc.), hot air channel, fan and other components to provide hot air up to 200-800 degrees for the drying body. Different combustion devices are selected according to the fuel selected by the customer;
The available fuels are: sawdust, biomass pellets, coal, gasoline, diesel, natural gas, liquefied petroleum gas and clean hot air recovered from other devices;
The available burners: hand-burned furnace, continuous furnace, biomass furnace, light oil burner, heavy oil burner, and vaporization furnace, etc.;
3-2, the main body of the drying drum cylinder:
It is made of boiler plate or high-temperature alloy plate, and stainless steel is used for special requirements. The maximum diameter can reach Φ4000. The inside is cylindrical and is the main area for material drying; the lifting plate (or shovel) is installed inside, and the material is repeatedly thrown through a specific angle design to increase the contact area with the hot air medium; some models of cylinders are designed with small holes or diversion structures on the surface to optimize the uniformity of hot air distribution.
According to the characteristics of the customer’s raw materials and production requirements, the cylinder can be designed into 3 layers (three-pass drum dryer), which effectively increases the drying area while extending the drying time, while increasing the utilization rate of heat, and can reduce the installation size to meet the special needs of different factories.
Feed/discharge end
Feed end: The feed end is connected to the heat source, and the feed port adopts a funnel-shaped structure. It can be equipped with spiral feeding or air lock feeding. While strictly sealing, it can also effectively control the uniformity and amount of feeding.
Discharge end: The discharge end is connected to the dust removal system. The structure is similar to the feed end. It can be equipped with spiral discharging or air lock discharging, which can effectively seal the cylinder and avoid heat loss.
3-3, Drive System
Drive part
The power is provided by the variable frequency motor. Through the reducer, coupling and large ring gear-pinion structure, the high-speed rotation is converted into the low-speed uniform rotation of the drum. Some equipment adopts the self-aligning tug design to reduce transmission wear and energy consumption.
Support and stability part
The roller frame and the roller: welded by medium carbon steel plate, support the weight of the drum and ensure smooth rotation.
Roller belt: fixed on both sides of the cylinder, cooperate with the roller to achieve stable rotation.
3-4. Dust removal system:
According to the environmental protection requirements on site, the dust removal systems available are as follows:
– Cyclone dust collector;
– Pulse dust collector;
– Water curtain dust collector;
It can be used alone or in combination according to the working conditions;
3-5. PLC electronic control system
The PLC system can monitor and adjust the temperature of the hot air system, the temperature of the cylinder, and the speed and operating load of the monitoring system at any time, and provide real-time alarms to provide active protection for the system.
3-6. Other ancillary equipment:
The feeding and discharging device can choose a belt conveyor or a screw conveyor, which can be scientifically selected according to the characteristics of the material.
4. What is the working principle of the rotary drum dryer:
The wet material is sent to the feed port by a belt conveyor or a screw conveyor, and then passes through the feed port drum dryer. At the same time, the hot air enters the dryer from the feed end port and contacts the material in the downstream. As the drying drum rotates, the material is continuously lifted up by the lifting plate in the drum, and is fully contacted with the hot air during the falling process until it reaches the tail end of the dryer and is discharged from the discharge port. The material is transported to the next stage by the conveying device; the water vapor and dust generated during the drying process are collected and filtered in the dust collector under the action of the fan, and the water vapor is directly discharged.
What are the categories of rotary drum dryers?
As a non-standard customized equipment, drum dryers have different names and uses according to different naming habits;
According to the structure: single-pass dryer, three-pass dryer;
According to the use, it can be divided into: coal slime dryer, sawdust dryer, distiller’s grains dryer, mineral powder dryer, sludge dryer, etc.
Different drying equipment has its own characteristics, which requires special design and adjustment, matching different heat sources, and the effects are often different. It needs to be designed and reasonably selected to achieve high efficiency and high yield.
6. What are the technical parameters of the rotary drum dryer?
5-1 Single Layer Rotary Drumer Dryer
5-2 Three Layer Rotary Drum Dryer
FAQ's
Frequently Asked Questions
What products does your manufacturing company produce?
We provide a wide range of machinery, including briquette machines, mixers, dryers, and more, designed for various industrial applications.
What is the typical lead time for product delivery?
Lead times vary depending on the machine and customization options. Please contact us for specific timelines related to your order.
What materials can your briquette machines process?
Our briquette machines can process a variety of materials, including biomass, charcoal, and other organic waste products.
What are the energy requirements for your machines?
Each machine has specific energy requirements, which can be provided upon request. We aim to design energy-efficient solutions.
Request A Quote
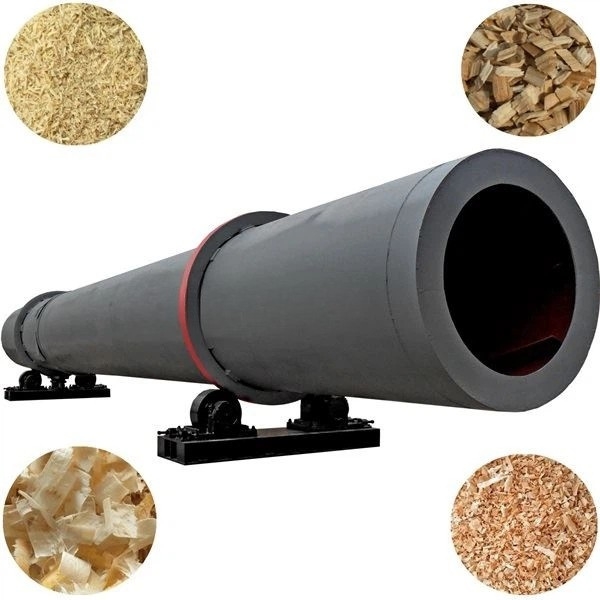
Drum Dryer
Drying moisture: from 60% to 1% of raw materials;
Output: 300 kg/hour-50,000 kg/hour
Applicable raw materials: mainly for drying powdered/granular materials with good fluidity, such as coal slime, sawdust, slag, mineral powder dust removal ash, etc.
Features:
- High dehydration efficiency: The rotary drum design allows the hot air flow to directly contact the surface of the material, combined with the rotation of the drum to achieve continuous tumbling and throwing of the material, greatly improving the heat exchange efficiency and shortening the drying time;
- Continuous 24h/30d operation, huge processing capacity: The rotary drum dryer adopts continuous operation to meet the needs of scale;
- Low energy consumption and wide practicality of heat source: It can accept different heat sources for heating or heat exchange, such as various biomass materials, coal, oil, gas, etc.;
- PLC automatic control: visible operation, checkable data, high degree of automation;
- Low operation and maintenance cost: The equipment is reasonably designed, simple in structure, and low in operation and maintenance costs.
- PDF DOWNLOAD