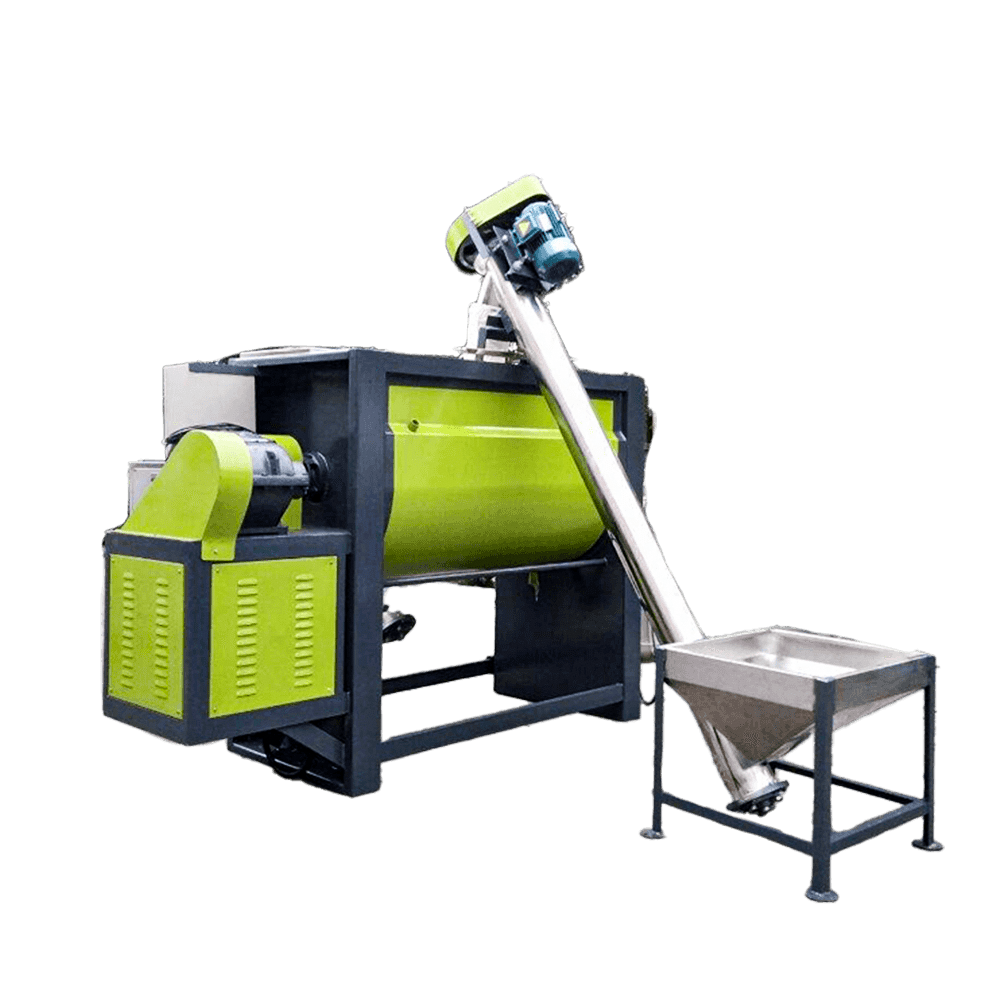
Double Screw Mixer
Processing Capacity: 0.5-3 cubic meters/time.
Application Range: Special design for charcoal powder with low bulk density, large dust ratio and high mixing uniformity requirements.
Features:
- High mixing efficiency: the mixing uniformity is more than 95%, and the running speed can be adjusted by PLC;
- The proportion and mixing time of the mixed materials can be controlled. When used in conjunction with the weighing system, the weighing and automatic unloading can be realized through PLC;
- Special customization: Special design for the characteristics of charcoal powder with low bulk density, large dust ratio and high mixing uniformity requirements;
- Low residue design: U-shaped cylinder + bottom discharge port, the residue is less than 1%;
- Strong durability: The spiral ribbon is made of wear-resistant alloy or carbon steel, and the service life can reach more than 5 years;
- PDF DOWNLOAD
Double-screw mixer, also known as horizontal spiral ribbon mixer, is a high-efficiency intermittent mixing equipment suitable for low bulk density powder, granules and solid-liquid mixing. Its core is to achieve dead-angle mixing of materials through the synergistic effect of internal and external spiral ribbons, and is widely used in carbon powder pelletizing production lines.
1. Main structure:
U-shaped cylinder: horizontal U-shaped structure, convenient for material circulation and less residue;
Double spiral ribbon: the outer spiral ribbon pushes the material from both sides to the center, and the inner spiral ribbon pushes in the opposite direction to form convection;
Transmission system: the motor drives the reducer to drive the main shaft to rotate, and some models support variable frequency speed regulation to meet different mixing needs.
Sealing device: the shaft end adopts a special sealing design to prevent dust leakage and meet the clean production standards.
2. Optional configuration:
Spraying/adhesive addition system: used to add liquid components (such as liquid additives/water, etc.)/powdered adhesives to achieve uniform solid-liquid mixing;
Heating/cooling jacket: the outer layer of the cylinder is equipped with a jacket to meet the material temperature control requirements;
Steam inlet channel: to meet the needs of heating the mixture by steam in some areas in winter;
The shape of the cylinder can be customized: U-shaped structure or cylindrical structure.
3. Working Principle
The double-screw mixer achieves efficient mixing through the triple mechanisms of convection, shearing and diffusion:
3-1: Convection mixing
The outer spiral ribbon pushes the material to gather towards the center, and the inner spiral ribbon diffuses in the opposite direction, forming a two-way material flow and eliminating dead corners of mixing.
3-2: Shear mixing
The shear force is generated between the edge of the spiral ribbon and the material, effectively breaking up agglomerated particles (such as agglomerated dry powder, sticky materials);
3-3: Diffusion mixing
At the microscopic level, the material is homogeneously distributed due to mechanical vibration and collision, which is suitable for fine materials (such as lithium battery positive electrode materials).
FAQ's
Frequently Asked Questions
What products does your manufacturing company produce?
We provide a wide range of machinery, including briquette machines, mixers, dryers, and more, designed for various industrial applications.
What is the typical lead time for product delivery?
Lead times vary depending on the machine and customization options. Please contact us for specific timelines related to your order.
What materials can your briquette machines process?
Our briquette machines can process a variety of materials, including biomass, charcoal, and other organic waste products.
What are the energy requirements for your machines?
Each machine has specific energy requirements, which can be provided upon request. We aim to design energy-efficient solutions.
Request A Quote
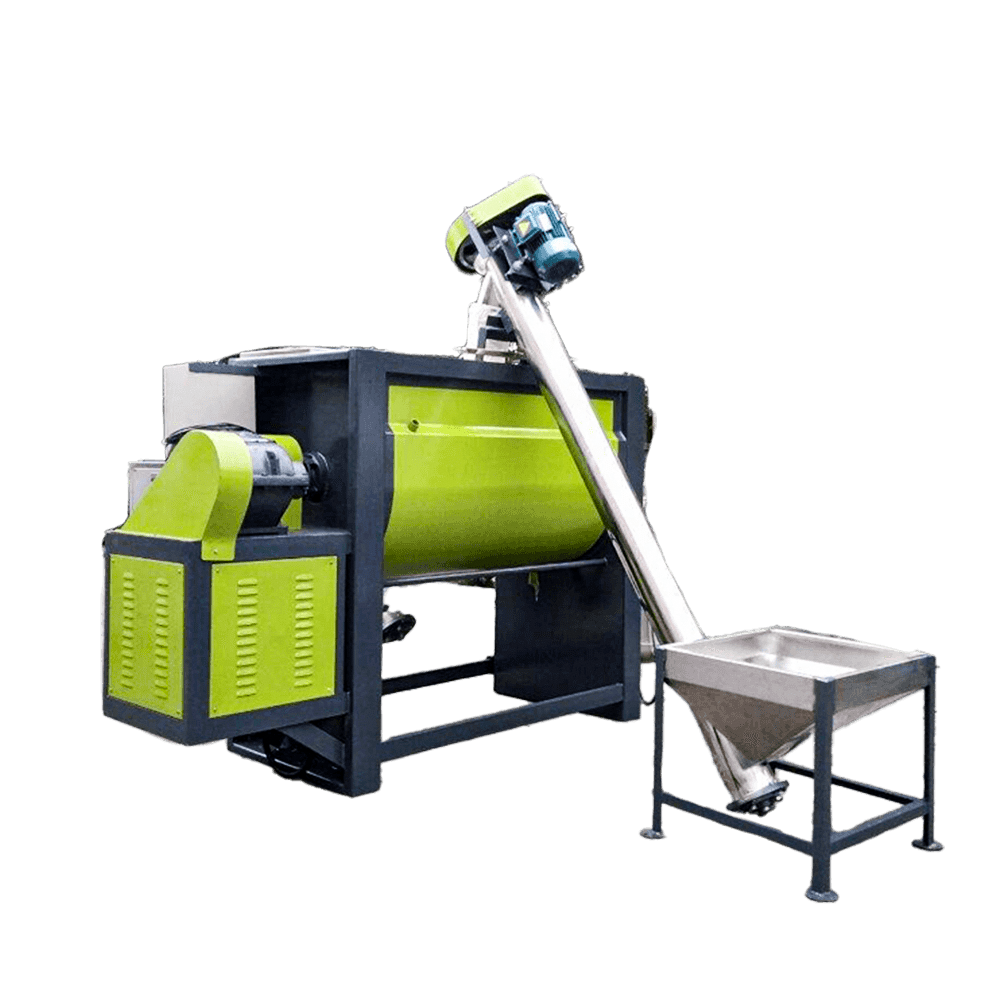
Double Screw Mixer
Processing Capacity: 0.5-3 cubic meters/time.
Application Range: Special design for charcoal powder with low bulk density, large dust ratio and high mixing uniformity requirements.
Features:
- High mixing efficiency: the mixing uniformity is more than 95%, and the running speed can be adjusted by PLC;
- The proportion and mixing time of the mixed materials can be controlled. When used in conjunction with the weighing system, the weighing and automatic unloading can be realized through PLC;
- Special customization: Special design for the characteristics of charcoal powder with low bulk density, large dust ratio and high mixing uniformity requirements;
- Low residue design: U-shaped cylinder + bottom discharge port, the residue is less than 1%;
- Strong durability: The spiral ribbon is made of wear-resistant alloy or carbon steel, and the service life can reach more than 5 years;
- PDF DOWNLOAD
Screw Mixer
Screw mixer use internal and external multi-layer spiral mixing system, no mixing dead angle, fast mixing speed and evenly. Following driven of mixing shaft, internal and external spiral push the materials moving to the two side from center, center spiral push the materials to center from two sides , mixing the materials up and down, right and left. Meanwhile, some of the materials will be pushed by spiral following the towards of shaft. So the materials will be mixed evenly and fast.
Advantage of Screw Mixer
1, U type host, running stable, low noise, longer service life, easy installation, widely applicable
2, Screw loading device, fast loading speed
3, Maintenance gate left, easy to do clean work
4, Fast mixing speed, and mixing result more than 96%
5, Less investment, less space request, easy operation
6, Easy to control the binders quantity
7, Suitable for powder and liquid binders
8, Excellent mixing result