Support
Briquette Machinery & Mesh Belt Dryer Manufacturer
Services
DMS has established a complete management system from initial consultation, solution design, on-site visit, machine preparation and shipment to after-sales feedback, to effectively ensure rapid and timely transmission of information so that the specialized services and technical supports can be provided by the correct persons at the correct time.
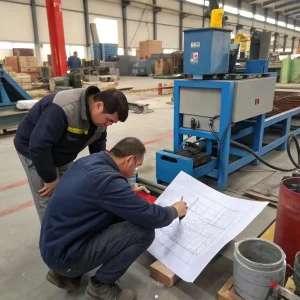
30
Rapid reply within 30 minutes
To the issue you consult about, or the feedback from you, we are sure to make reply within 30 minutes to have effective communication.
24
Providing solution within 24 hours
According to the results of communication with you, we will, within 24 hours, provide a design solution, or a solution handling your feedback.
72
Dispatching engineers within 24/72 hours
If we decide to dispatch engineers to support your production, we commit ourselves to dispatching them within 24/72 hours domestically/abroad.
Four Steps Ensuring Safety
Efficiency of machine preparation and shipment

Checking order
With the sales contract, the order tracking clerk checks the models and quantities of machine and spare parts for machine preparation.

Quality test before delivery
Upon completion of the manufacturing of equipment, the quality inspector strictly checks quality of every machine with the checklist.

Check items when packing
Before packaging and shipment, the order tracking clerk checks the packaged items again with the packing list to avoid loss of items.

Packaging and transport
Professional packaging and modular solution of transportation guarantee the safe and smooth delivery.
Installation & Commissioning
Depending on customers’ needs, DMS’s installation engineers can provide on-site guidance in infrastructure construction, equipment installation and commissioning, as well as trial operation of entire production line. If technical items meet the design criteria, the customer will sign the certificate of conformity.

Installation preparation stage
Checking the purchase order; counting the items with the purchase order; checking the dimensions including evaluations of the items with the drawings.

Equipment commissioning stage
Check the equipment again. Before putting the project into use, the commissioning is done to ensure the operation to meet production needs.

Equipment installation stage
Install the main equipment and accessories according to the installation drawing.

Project acceptance stage
Provide the certificates of conformity and test reports for main materials as well as the documents of equipment (user's instructions, certificate of conformity, etc).
Quality Warranty
DMS provides high quality and reliable briquette combustion equipment for industrial production and residents’ life.
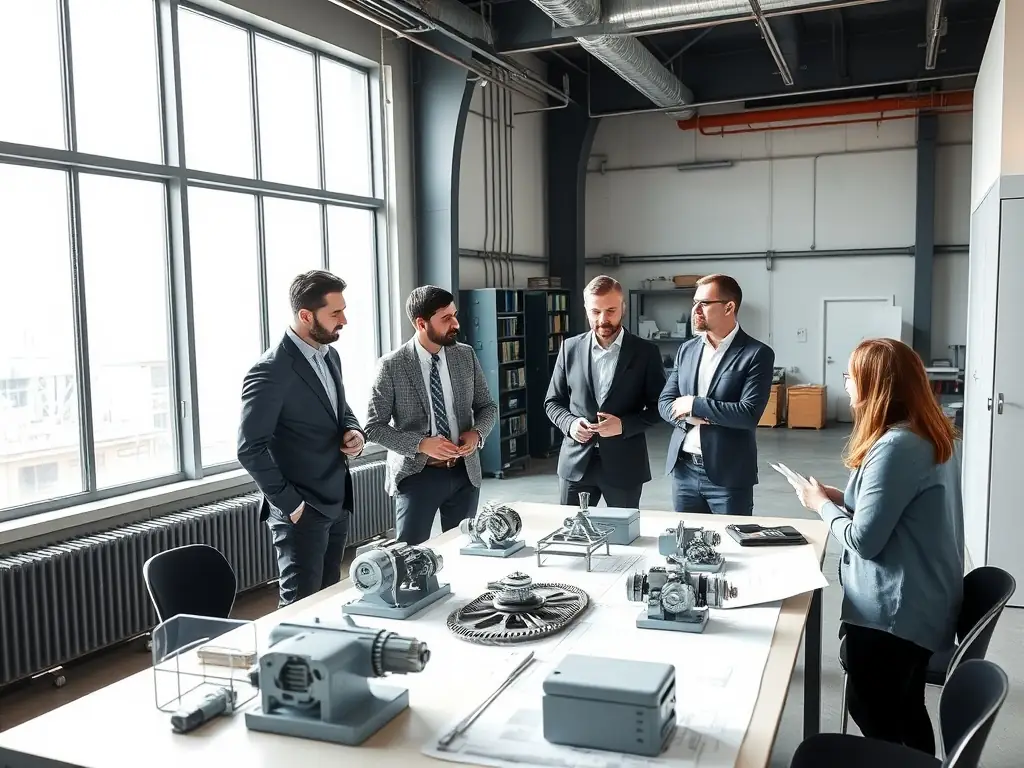
Terms of Warranty
DMS provides a six-month warranty (excluding vulnerable parts) with free repairs, replacements, and returns. Party B bears related costs, including freight and technician accommodation. Party A is not liable for indirect losses but will provide support if Party B covers accommodation.
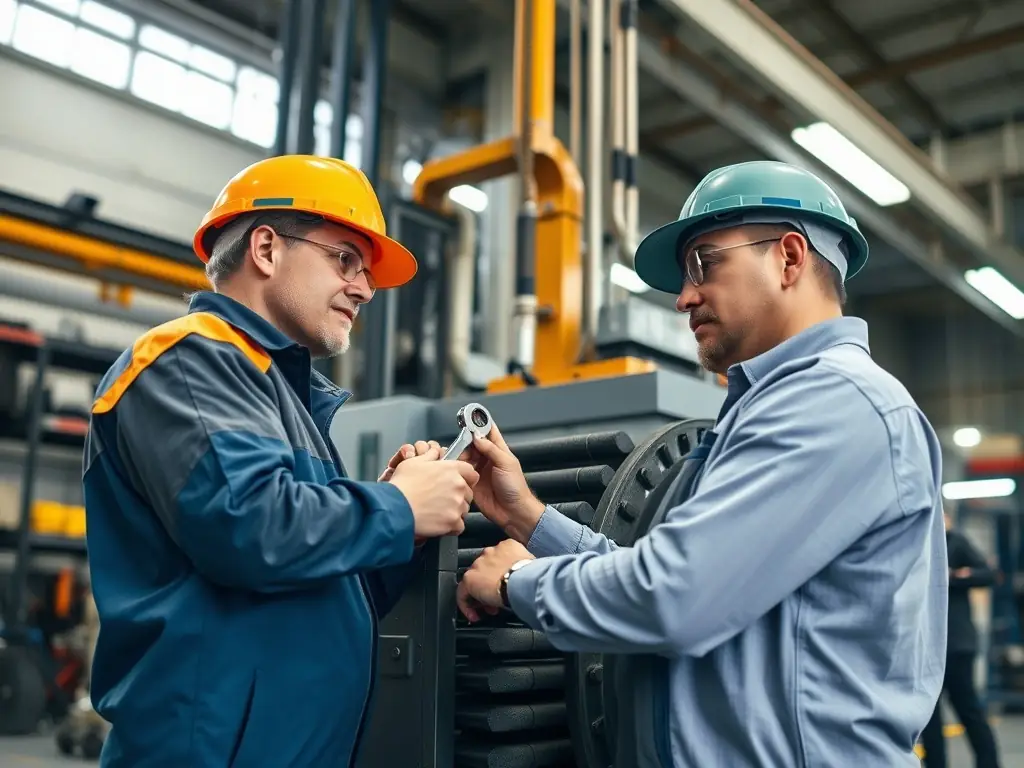
One-year quality warranty
DMS provides a one-year warranty for its equipment after project acceptance. Users must present invoices and vouchers. Quality-related repair costs are covered by DMS per the Installation Confirmation Voucher and User Information Card.
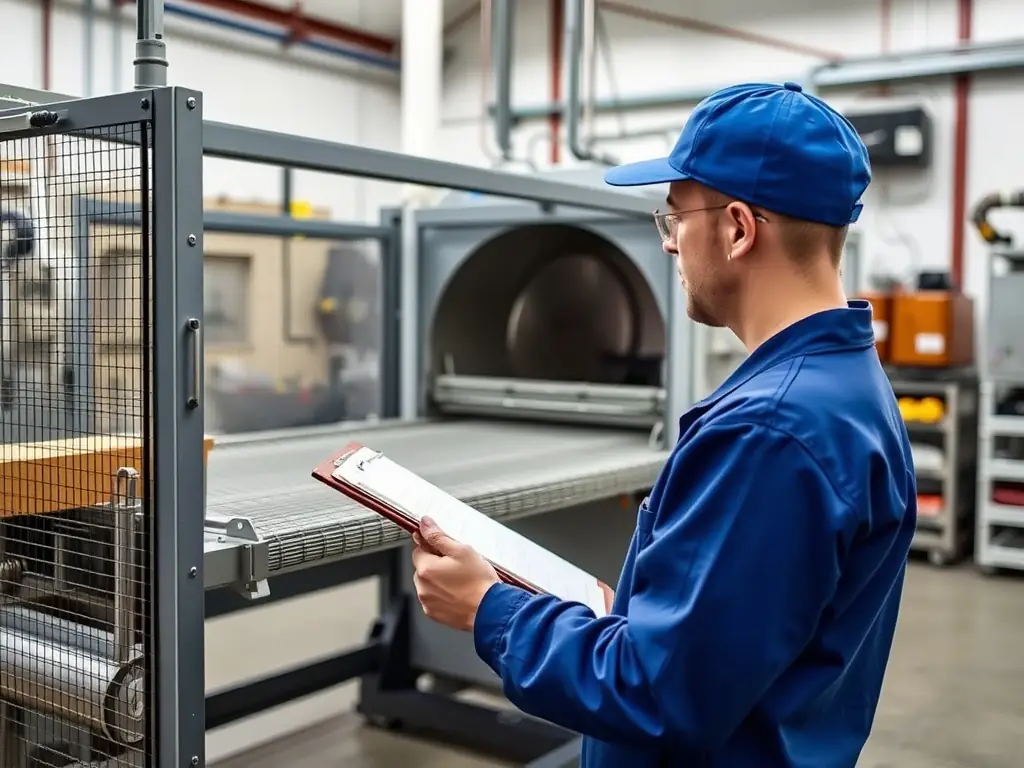
Quick Complaint Handling
For complaints about production line operation from customers, we undertake to complete problem identification and solution offering within 24 hours, and solve the problem within 3/10 days for domestic/foreign customers.
FAQ's
Frequently Asked Questions
What products does your manufacturing company produce?
We provide a wide range of machinery, including briquette machines, mixers, dryers, and more, designed for various industrial applications.
What is the typical lead time for product delivery?
Lead times vary depending on the machine and customization options. Please contact us for specific timelines related to your order.
What materials can your briquette machines process?
Our briquette machines can process a variety of materials, including biomass, charcoal, and other organic waste products.
What are the energy requirements for your machines?
Each machine has specific energy requirements, which can be provided upon request. We aim to design energy-efficient solutions.